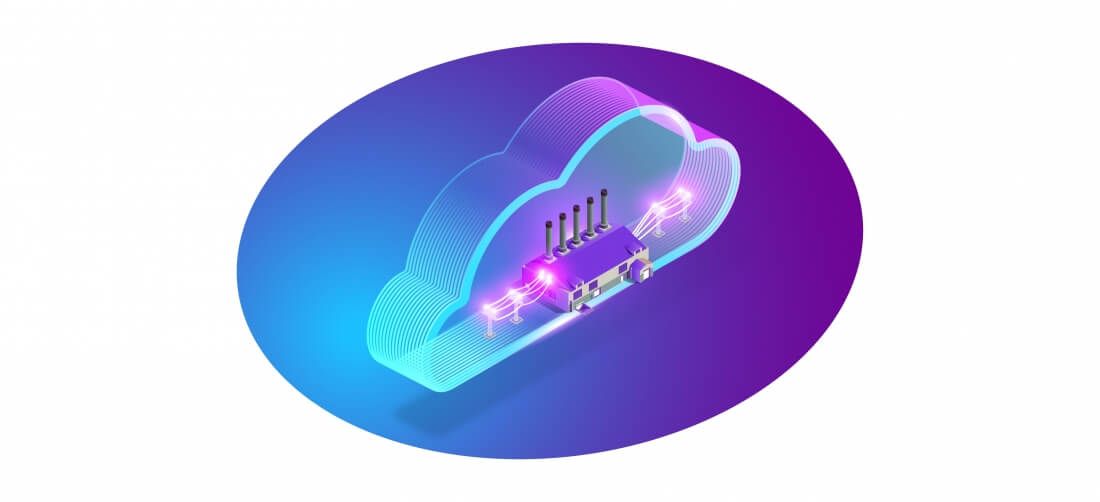
This article has been prepared by Gcore for informational purposes only and is based on data from open sources.
Clouds are becoming increasingly popular in the energy and industry sectors.
This is due to the modernization and digital transformation of enterprises around the world that strive to increase their efficiency and improve competitiveness.
Modern clouds provide a number of benefits:
- They accelerate the development of specialized applications and systems for collecting and analyzing production data.
- They provide fast and easy access to computing power and scaling virtual infrastructure.
- They monitor production processes in real time and controlling their efficiency.
- They ensure the stable and safe operation of enterprises during peak loads or unplanned equipment failure.
- They reduce IT infrastructure costs.
Let’s take a closer look at some scenarios in which cloud technologies can be applied in energy and industry.
Accelerated application development
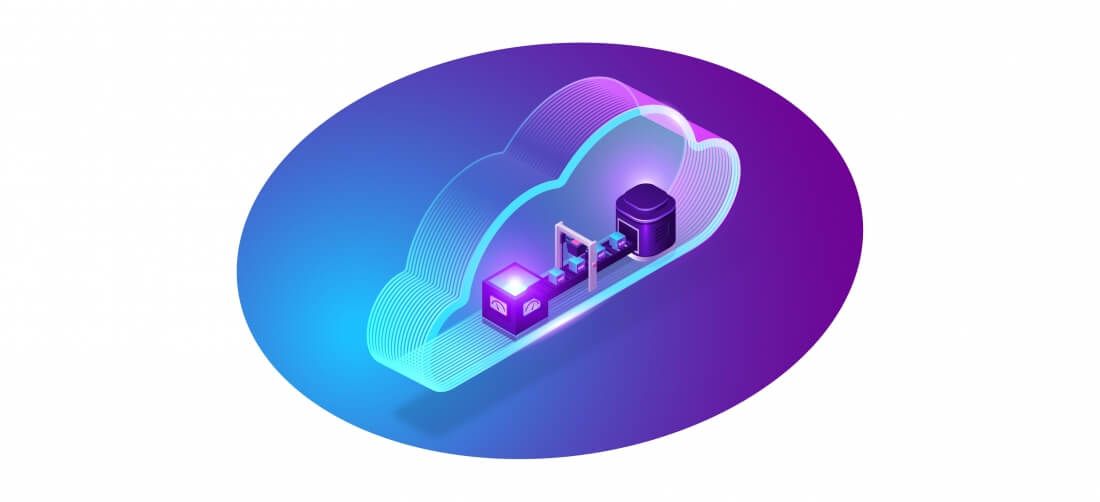
Cloud technologies reduce the time and cost of introducing new services that enable businesses to upgrade their production facilities or offer customers new product lines.
Automation and data management
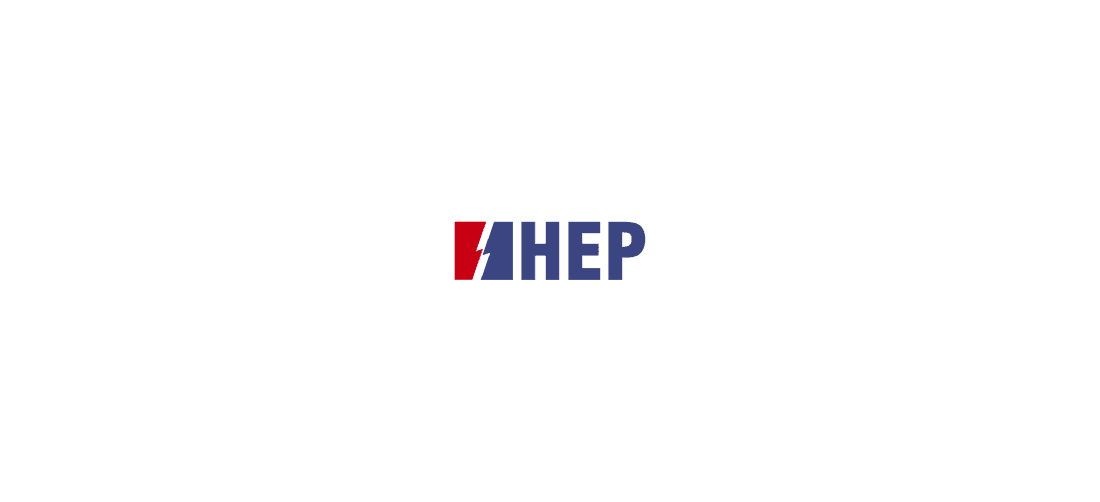
HEP, Croatia’s national energy company, faced the challenge of providing computing resources needed by businesses too slowly during the digital transformation process.
This significantly delayed the implementation of new projects. Migration to the cloud has allowed HEP to significantly speed up the development and testing of the required applications by automating many routine operations.
The first project in the cloud was the development of the Coal Information System, which is used for managing data on coal reserves at the Plomin thermal power plant. The task was to provide the managing company and the thermal power plant with accurate data on coal supplies and its current stock, as well as to provide a contract management tool.
Based on the results of the first two months in the cloud, HEP’s IT department saw an acceleration of releasing new features and updates for the application by over 50%. The HEP development team now has a ready-to-run environment without the hassle of purchasing and configuring hardware and software. Since implementing the cloud development process, HEP has noted increased savings and reduced risks thanks to standardized architecture and processes.
Peak load management
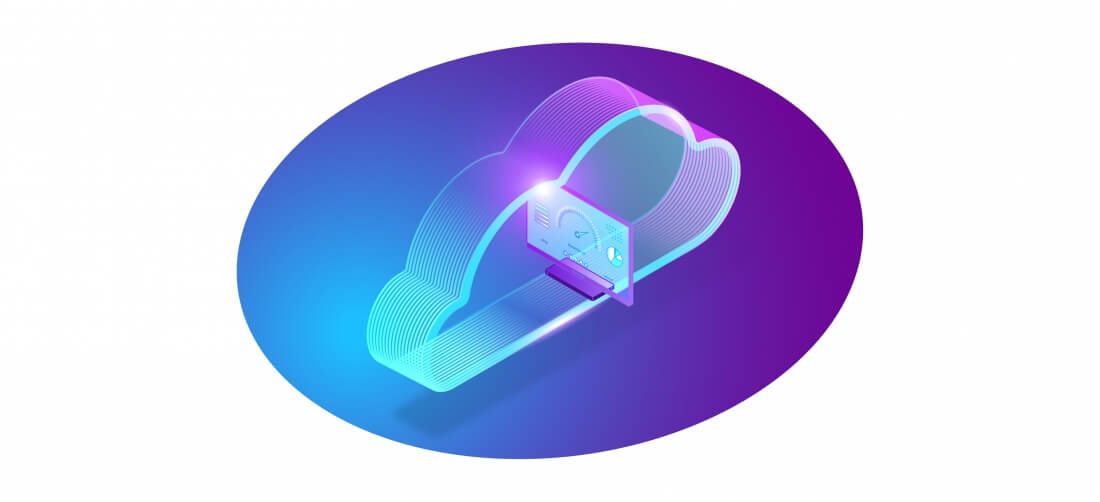
Cloud technologies provide quick access to additional computing power during sharp increases in the amount of data generated by the enterprise.
Similar situations arise when new production lines or instrument systems are connected, where sensors record the main parameters of the equipment (for example, temperature and pressure).
Uneven load distribution is a typical issue caused by, for example, peaks and troughs in electrical power consumption. Cloud-based virtual power plants help optimize infrastructure performance. Renewable energy systems (for example, solar or wind power plants) always have one more problem—uneven power generation due to changes in weather conditions.
Tesla’s virtual power plant
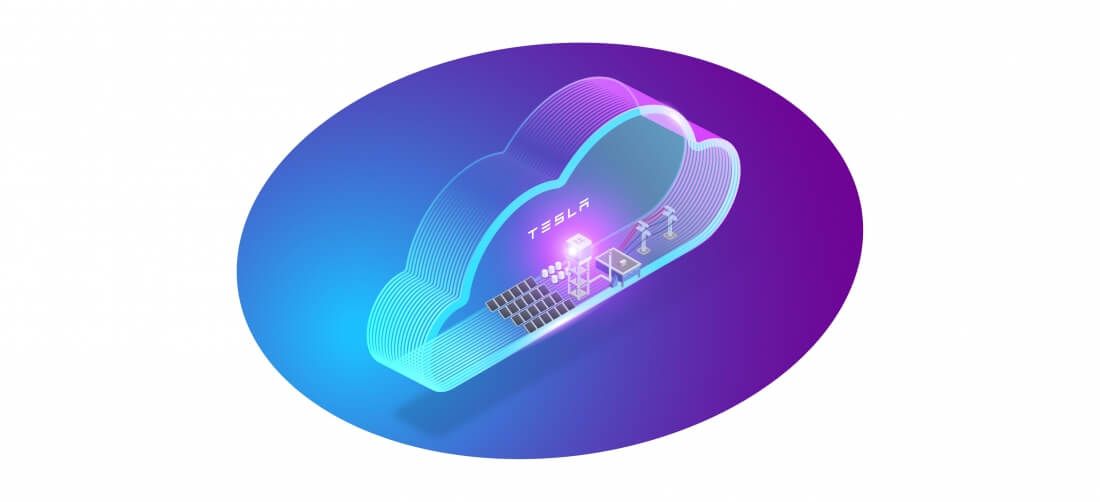
Tesla is implementing the world’s largest virtual power plant project: 50,000 solar and storage batteries are connected to provide a sustainable power supply to South Australia.
In the same region, the company has connected the largest energy storage facility at the Hornsdale wind farm. The optimal distribution of energy among consumers is ensured by a cloud platform.
Telemetry systems monitor the current state of energy infrastructure elements such as batteries, inverters, and chargers. The collected data is then processed in the cloud. Software models are then created. They are digital twins used to predict energy consumption and control system peripherals. The workload between industrial applications is distributed by Kubernetes clusters, providing fault tolerance for the virtual power plant.
AI load simulation
The Gcore AI Platform is suitable for simulating the peak loads of power systems. It integrates a number of data acquisition and processing tools, such as Kafka, Storm, Spark, PySpark, PostgreSQL, MS SQL, Oracle, and MongoDB.
Employing additional computing power during peak periods and shutting down unnecessary virtual machines when the load decreases are carried out in the cloud in just a few minutes.
The pay-as-you-go model allows you to pay only for the resources consumed with per-minute billing.
Disaster recovery
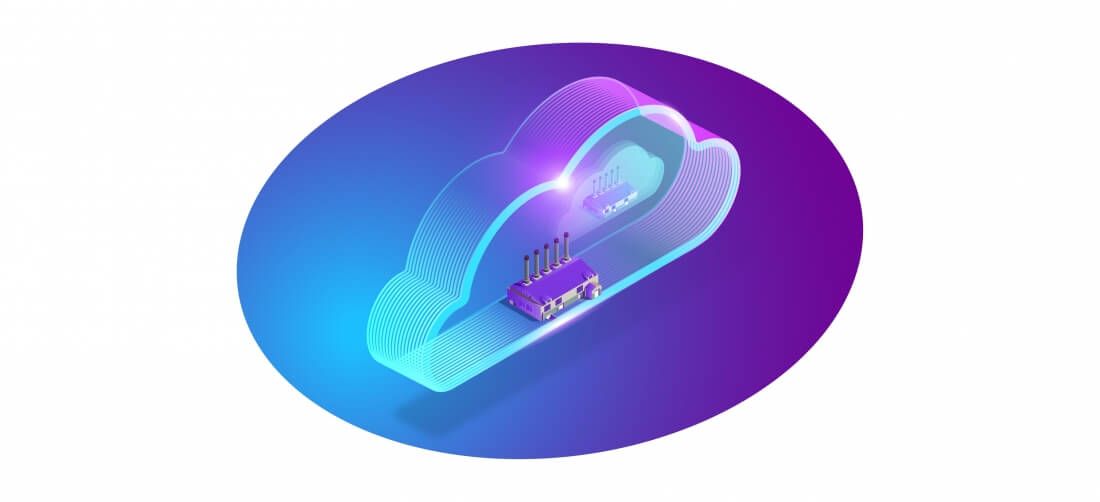
Cloud computing lowers enterprise costs in the event of emergencies related to control and monitoring system failures, equipment failures, data loss, and personnel errors. Companies receive the ability to use additional computing resources in emergency situations, create data backups, and automatically recover interrupted processes.
By switching to a cloud-based backup and disaster recovery solution, the oil and gas company Ultra Petroleum has cut its IT infrastructure costs by 50%. Implementing the new system took less than 8 hours.
In the Gcore cloud, disaster recovery is provided as a service: payments are required only for the active use of virtual machines, the need for which arises when testing equipment fault tolerance or in the occurrence of immediate failures in its operation. The system is easily scalable, allowing new applications to be introduced as needed. If there’s an incident, the complete recovery of any interrupted processes is carried out in just a few minutes.
Big data and artificial intelligence
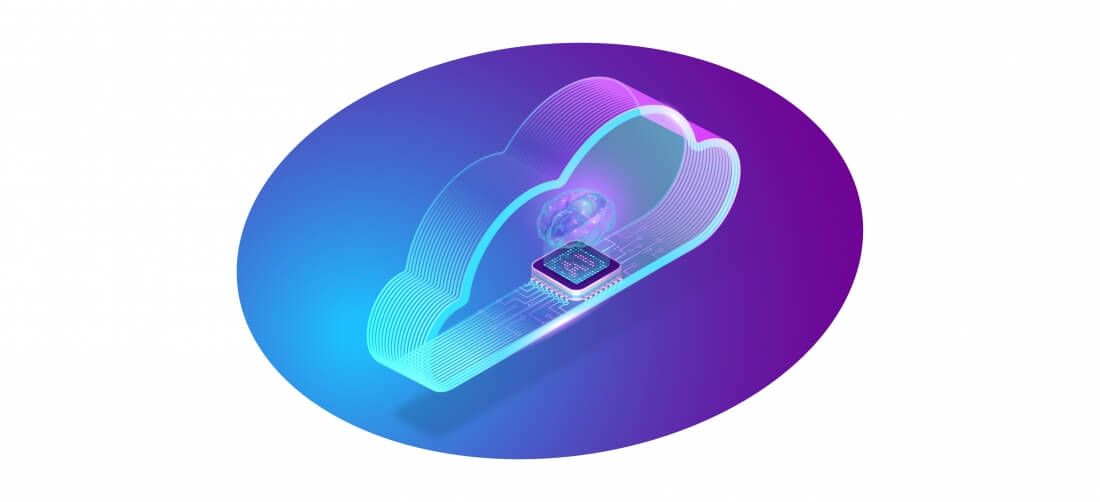
For modern industrial and energy companies, the ability to work with big data is becoming a key competitive factor. This requires the implementation of applications for data analysis, including those based on artificial intelligence.
Cloud infrastructure can help reduce the time it takes to develop, test, and deploy these applications and ensure they run smoothly.
Oil and gas
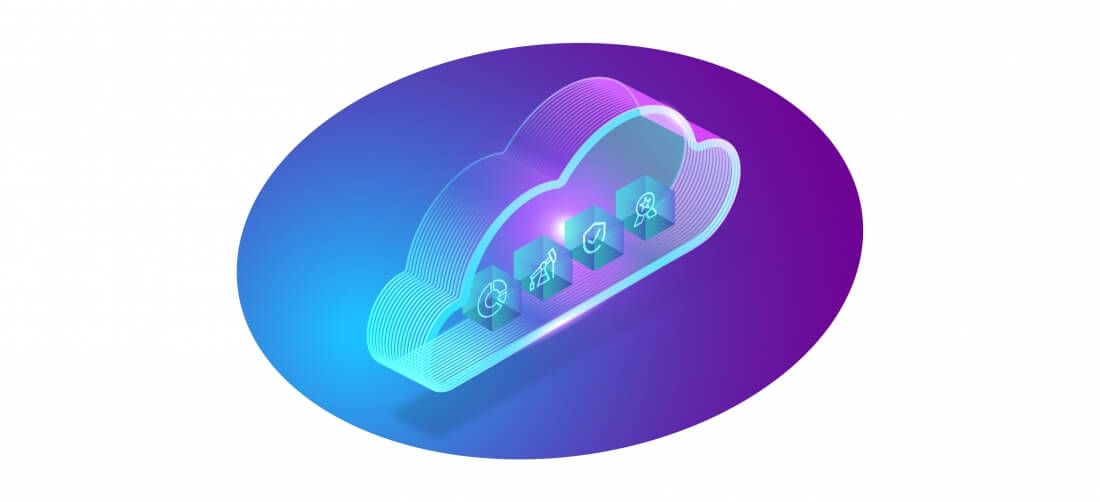
Shell is developing a number of projects based on a cloud platform with artificial intelligence.
Predictive maintenance. Wired and wireless sensors collect data about the current state of oil production and refining equipment, for example, valves and compressors. Using information about changes in temperature and pressure in different parts, the machine learning algorithms predict in advance when they need to be replaced. The solution is applied at 23 of the company’s facilities (refineries and offshore oil platforms), allowing them to avoid disruptions of their work. Shell estimates that predictive maintenance at its Pernis plant in the Netherlands has already saved the company several million dollars.
Searching for new oil and gas fields. Machine learning algorithms reduce the time of processing seismic data from the ocean shelf by 80%. In land drilling, artificial intelligence is used to accurately determine oil well contours and reduce wear on drilling rigs.
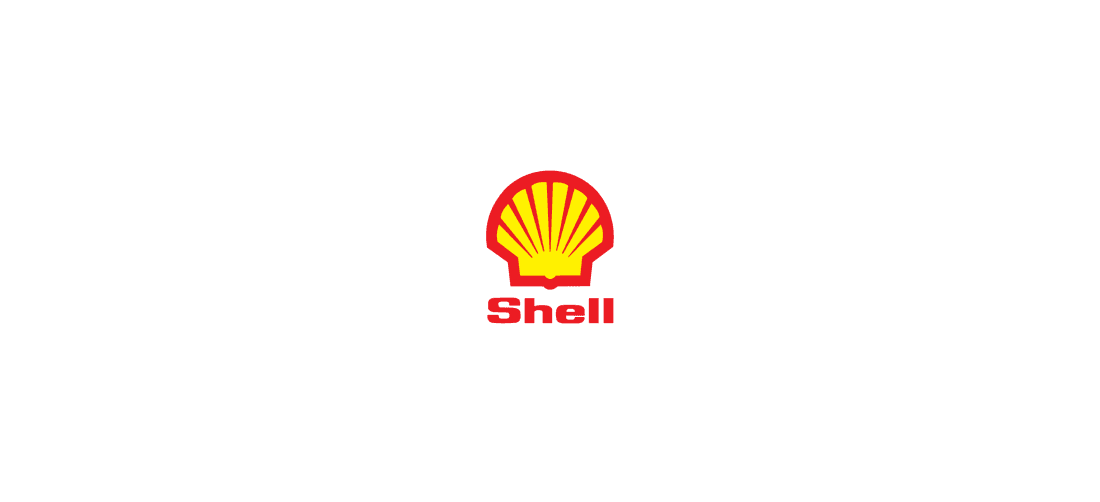
Security. Shell filling stations in Thailand and Singapore are equipped with video analysis systems. Artificial intelligence detects smoking and alerts employees to take action to prevent fires and explosions. In the future, Shell plans to use similar systems to ensure safety at its other facilities, for example, to monitor the condition of underwater equipment or the availability of protective overalls for oil workers.
Improved quality of service. Artificial Intelligence analyzes data from previous orders made by Shell customers, helping to develop personalized offers and loyalty programs.
Electrical engineering
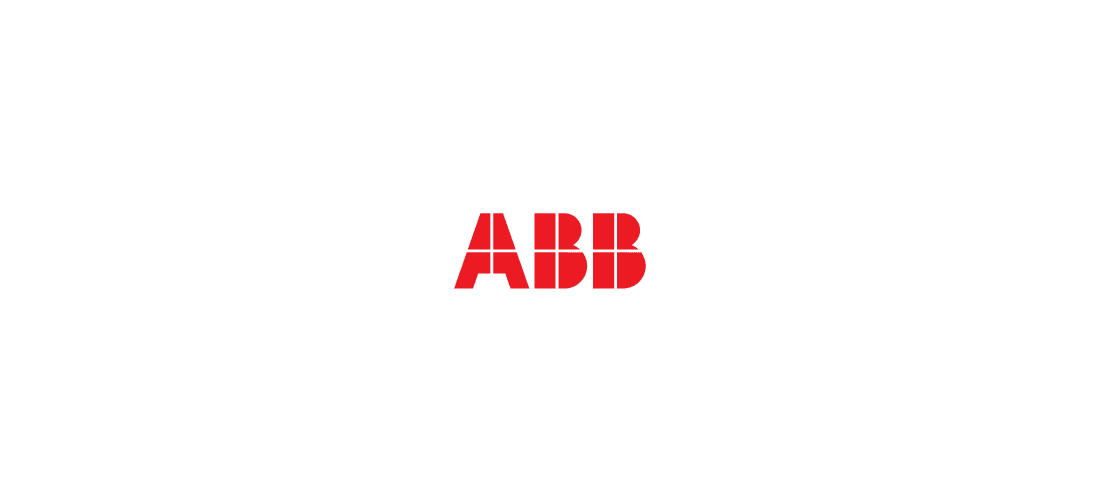
ABB is making its energy infrastructure sustainable by monitoring inverters and transformers with AI cloud digital twins. A low-cost solution based on image recognition technologies has been developed for customers who wish to ensure security in an industrial enterprise. Neural networks using the TensorFlow and Keras machine learning tools detect corrosion on electrical wiring and assess of the risk of it failing.
The development and testing of services based on artificial intelligence is a promising area of investment for industrial and energy companies. It allows them to upgrade production facilities and create new services. The cloud AI Platform with integrated machine learning tools such as TensorFlow, TensorRT, OpenVINO, Keras, fast.ai, PyTorch, and BigDL will also help speed up this process with minimal IT infrastructure costs.
Internet of things
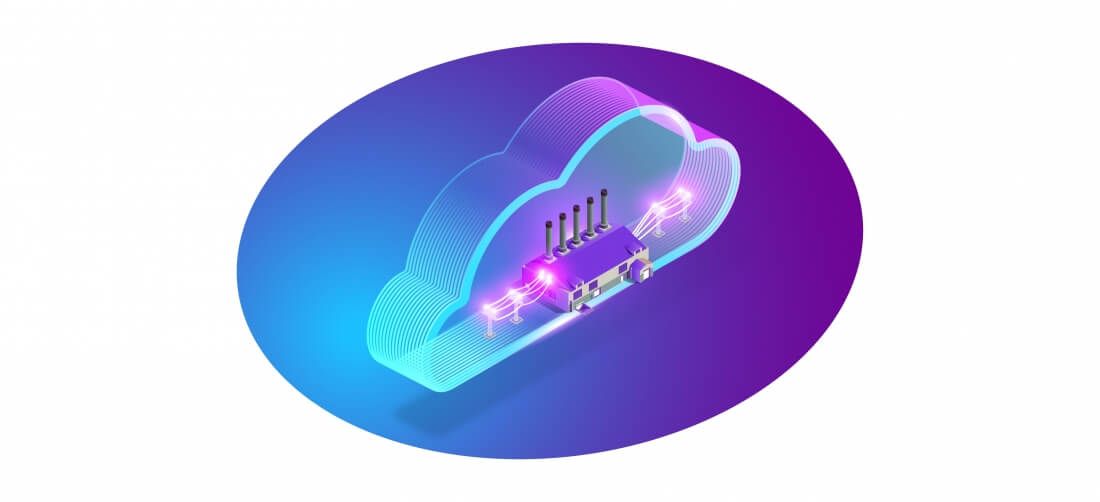
Cloud technologies ensure functioning of industrial internet of things systems. The centralized management of smart manufacturing is carried out through the continuous collection and analysis of data on production and logistics processes in an enterprise.
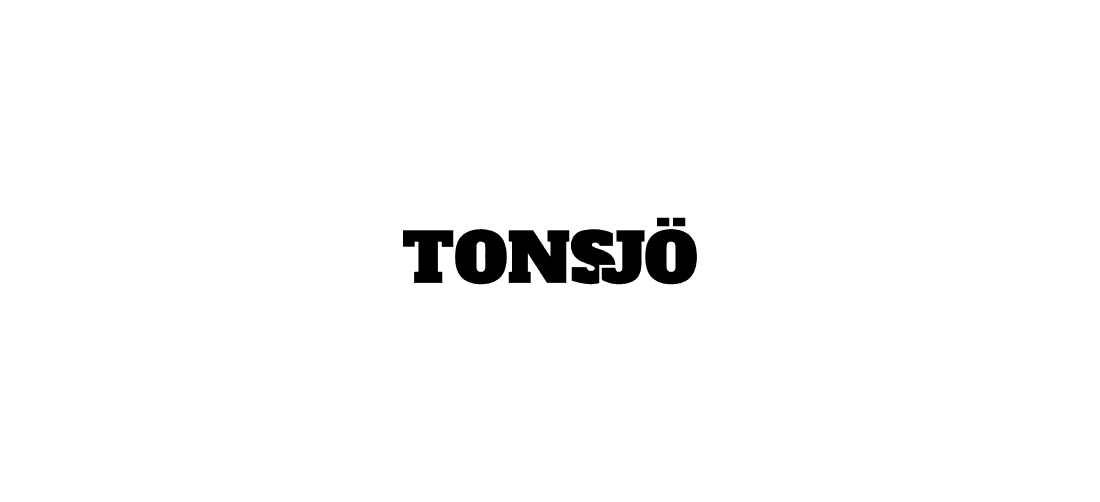
Tonsjö uses a cloud to automate its metal production. Sensors connected to milling, turning, and boring machines and industrial robots monitor equipment health, speed, and efficiency in real time.
The collected information is stored and processed in the cloud, along with CRM data and financial records. The digital monitors installed at the enterprise display warnings about the risks of equipment malfunction and up-to-date statistics. Tonsjö estimates that production from its cloud-connected production lines has grown by 4%.
The Gcore team has many years of expertise and successful experience in the design, construction, and operation of cloud systems of various types—private, public, and hybrid. Our clouds are reliably protected, withstand any peaks, and scale in minutes, which is especially important if you consider the challenges today’s industrial and energy companies meet. We offer an individual approach to each client. We’re ready to customize our solutions and add the necessary features upon request.
Vsevolod Vayner Gcore Cloud Platform Department Head
Are you looking for new solutions for the optimization and automation of production? Do you also want to reduce infrastructure costs?
Try our cloud services today or get started with a free consultation from one of our experts.
Related articles
Subscribe to our newsletter
Get the latest industry trends, exclusive insights, and Gcore updates delivered straight to your inbox.